I set aside, or tied to set aside, a weekend for assembling the canoe. The plan was to start early Saturday morning, tape the chine panels to the bottom, prime the edges, wait, apply putty, wait, fiberglass, sleep, get up early Sunday, and repeat with the upper panels. Well, it
was a nice plan.
Now for reality. Other responsibilities came up. But I did get a respectable amount done. First order of business - tape the seams. I tried to avoid using stitches for simplicity (I didn't want to fill holes). I used 3M low residue duct tape to tape the seams. It wasn't nearly as easy as it looked in the
free canoe plans. Those tutorials were produced by professionals, and this is my first project. Quickly, what I learned:
- Start with short lengths of tape spaced 12" to 18" apart.
- After the shape is close, tape the entire seam, pulling it into shape.
- Most important, stitches are necessary. I used one stitch at the top of the chine panel on the bow and stern. I wish I had used them every 12 or 18 inches, closer in tight bends.
Next, prime the wood with epoxy and putty the joints. This is my first experience puttying joints. Tricky! Someone on the
bateau forums suggested putting the fiberglass directly over the wet joints. This would probably save sanding the imperfect joints and spots of putty that are missed. This stuff dries like cement, and shreds sandpaper if you don't approach it slowly. Renee was a lot of help with the joints.
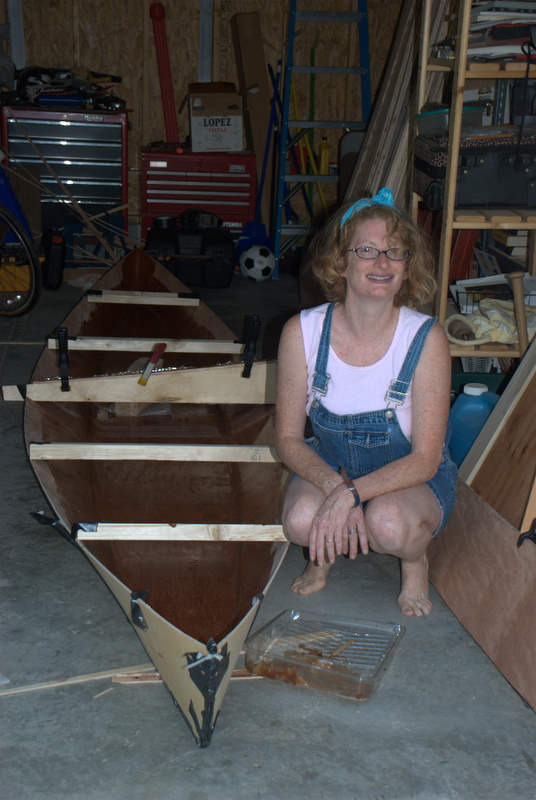
The hardest part to epoxy was the bow and stern. There is not adequate room to work. After trying to putty that narrow angle with a squeegee (messy) and my gloved fingers (more messy), I discovered the back and tip of a plastic spoon did an amazing job. I really dread sanding the mess I made in that area.

The next morning, I fiberglassed the inside bottom to chine panel joints and bow and stern joints. I put a thin coat of epoxy over the putty, and let it cure for an hour until sticky. While it was curing, I prepared the fiberglass tape by finding the center, and rolling to the center from each end, like a scroll. I carefully laid the fiberglass at the center joint, then rolled each way, lightly stretching the fiberglass as I went. The tackiness of the partially cured epoxy kept the tape in place. It also made realigning the tape a little messy. It would distort the tape a little to lift it.
I wet out the fiberglass using a 4" foam roller. It was a cool morning (for North Carolina), and everything went well. The
Marinepoxy wet out the fiberglass easily. I used 21 ounces of epoxy (seven 3 ounce batches) to wet out 34' of biaxial tape. I thought that I did a good job wetting out the tape without over saturating it, but maybe I did too good of a job - about 15% of the tape was a little epoxy starved. It is fixable, though.
It looks like an olive boat now.
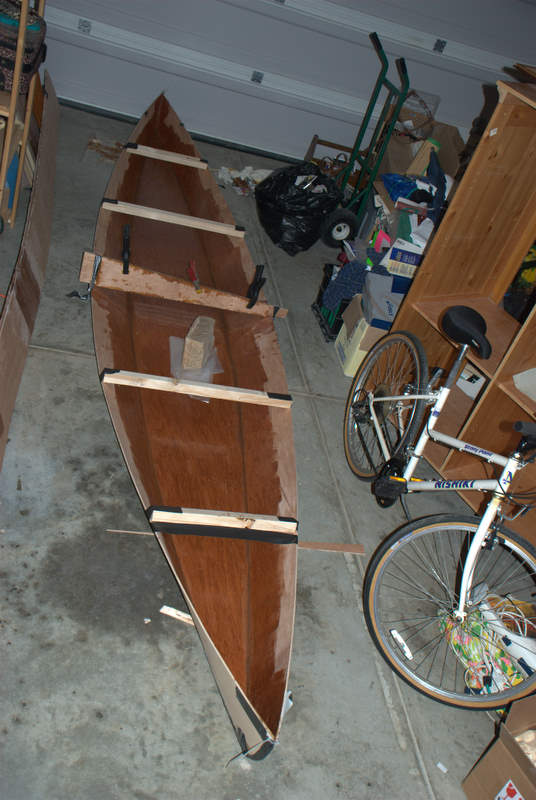
Next, the upper panels.